Antenna specialist HPS conquers new territory in RF applications with verification of innovative 3D production
HPS Space News
Even formerly very sceptical augurs of space travel now agree that the ability to largely automate the series production of lightweight components while minimizing raw materials and ensuring maximum reliability will have a significant impact on the future development of applicable technologies.
However, the central prerequisite for the implementation of such visions is still a very classic step-by-step verification, in this case of two materials selected by the HPS engineers using the new ESA standard ECSS-Q-ST-70-80C.
Given the future potential of such technology, the European and German space agencies have a primary interest in the success of the research at HPS and provided GSTP funding for the 3DPAN2 project: “3D-Printed Antenna 2” is a follow-up project to 3DPAN, which was completed five years ago and initially demonstrated the feasibility in principle of 3D-printed RF components.
The product objective was an extremely lightweight X-band antenna with a diameter of ~30cm for the data downlink of earth observation satellites. It was finally manufactured from the aluminum alloy SCALMALLOY at the sub-contractor APWORKS GmbH in Ottobrunn. In addition, a filigree feed support bracket made of titanium was manufactured for fold-out antennas by the long-standing HPS trusted partner, the Fraunhofer Institute for Material and Beam Technology IWS, Dresden, as a subcontractor.
Meanwhile, the respective designs and FE analyses, as well as their iterative optimization, were carried out by HPS in Munich itself.
The final tests delivered positive results that exceeded all expectations. This applied in particular to the RF performance of the X-band antenna in the Compensated Compact Range (Munich University of Applied Science MUAS). Resistance to vibration (sine + random) was also successfully demonstrated for both demonstrators at SGS GmbH, Geretsried: here too, everything went without complications, i.e. above all without damage or deformation. Even a final TVAC test (10 cycles between +120°C and – 120°C) showed no cracks or deformations on the demonstrators.
Olaf Stolz, the responsible project manager at HPS, summed up the project as follows: “The objectives of the verification processes were achieved without any restrictions: the additively manufactured demonstrators were 20% and 25% lighter than corresponding conventionally manufactured components – a well-known enormous advantage in space travel. There were no restrictions on qualification for space applications. We would like to thank our cooperation partners, especially Dr. Samira Gruber (Fraunhofer IWS) and Mr. Nicklas Schwab (APWORKS) for the extremely good and successful cooperation in the project, as well as ESA, in particular Ms. Isabel Olaya Leon, Technical Officer of the 3DPAN2 project.
HPS CEO Ernst K. Pfeiffer is delighted: “It is fantastic that we are already implementing 3D printed components with the technology results of the ESA GSTP program in current flight projects. A goal that we set 8 years ago and that is essential for the future market has now been achieved.”
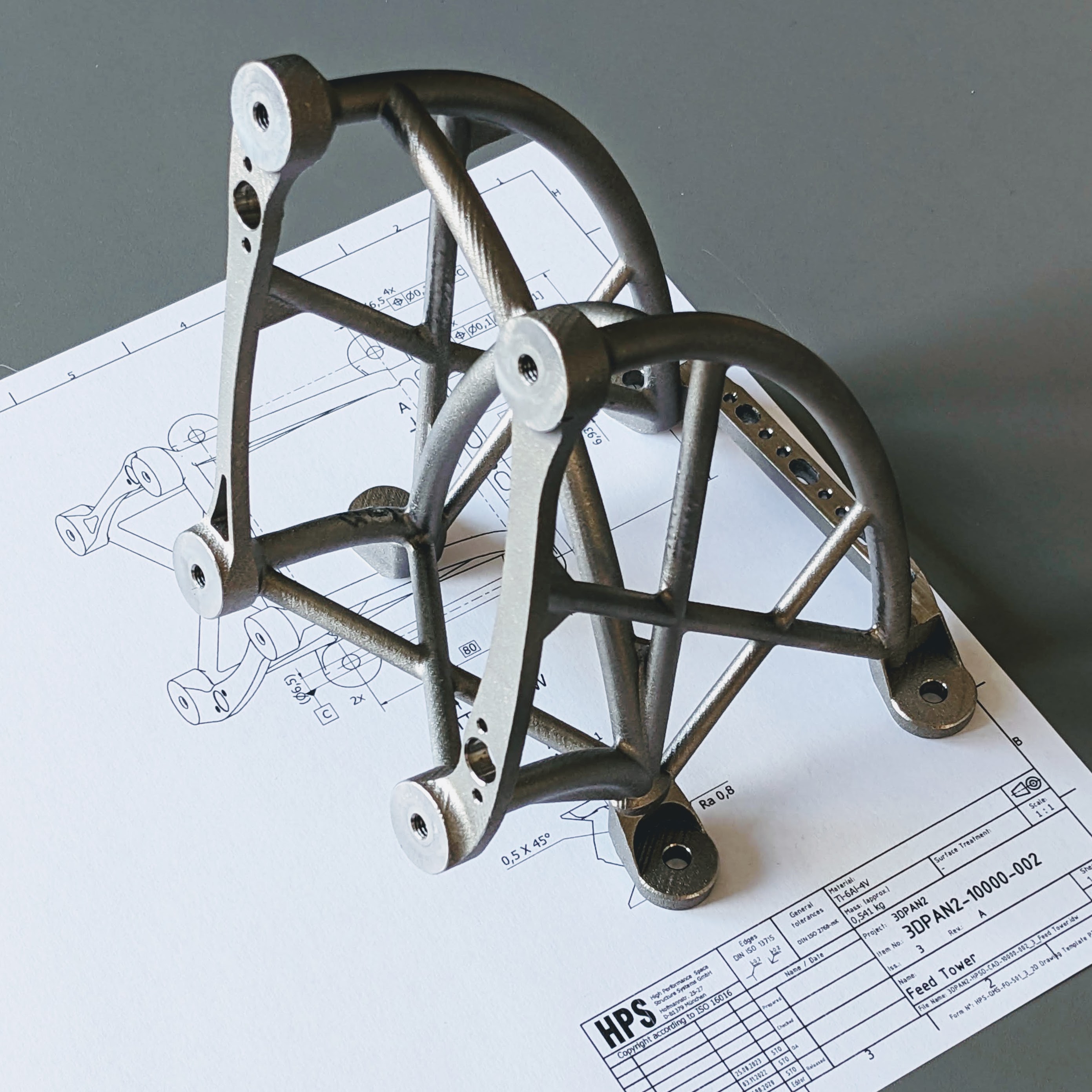
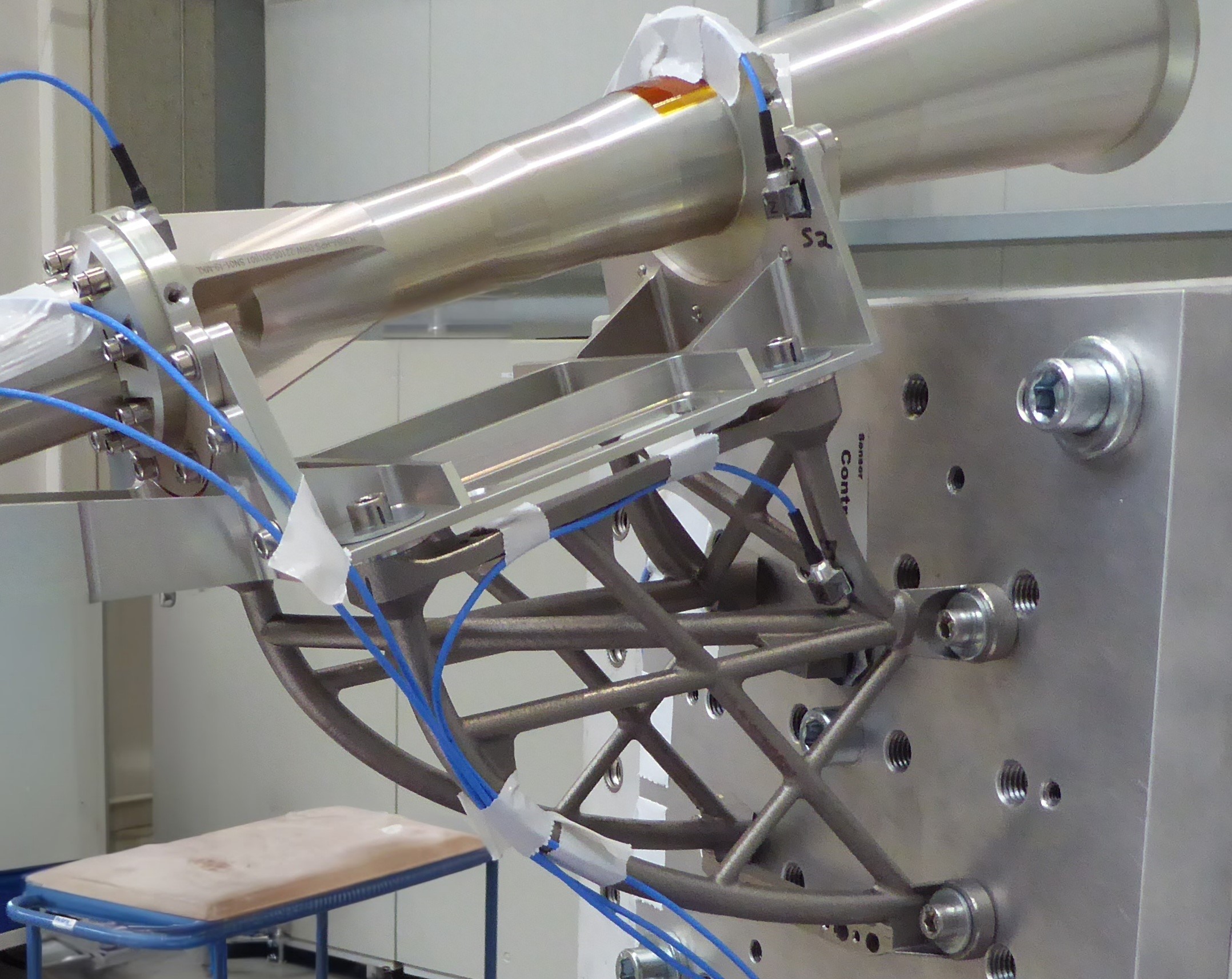
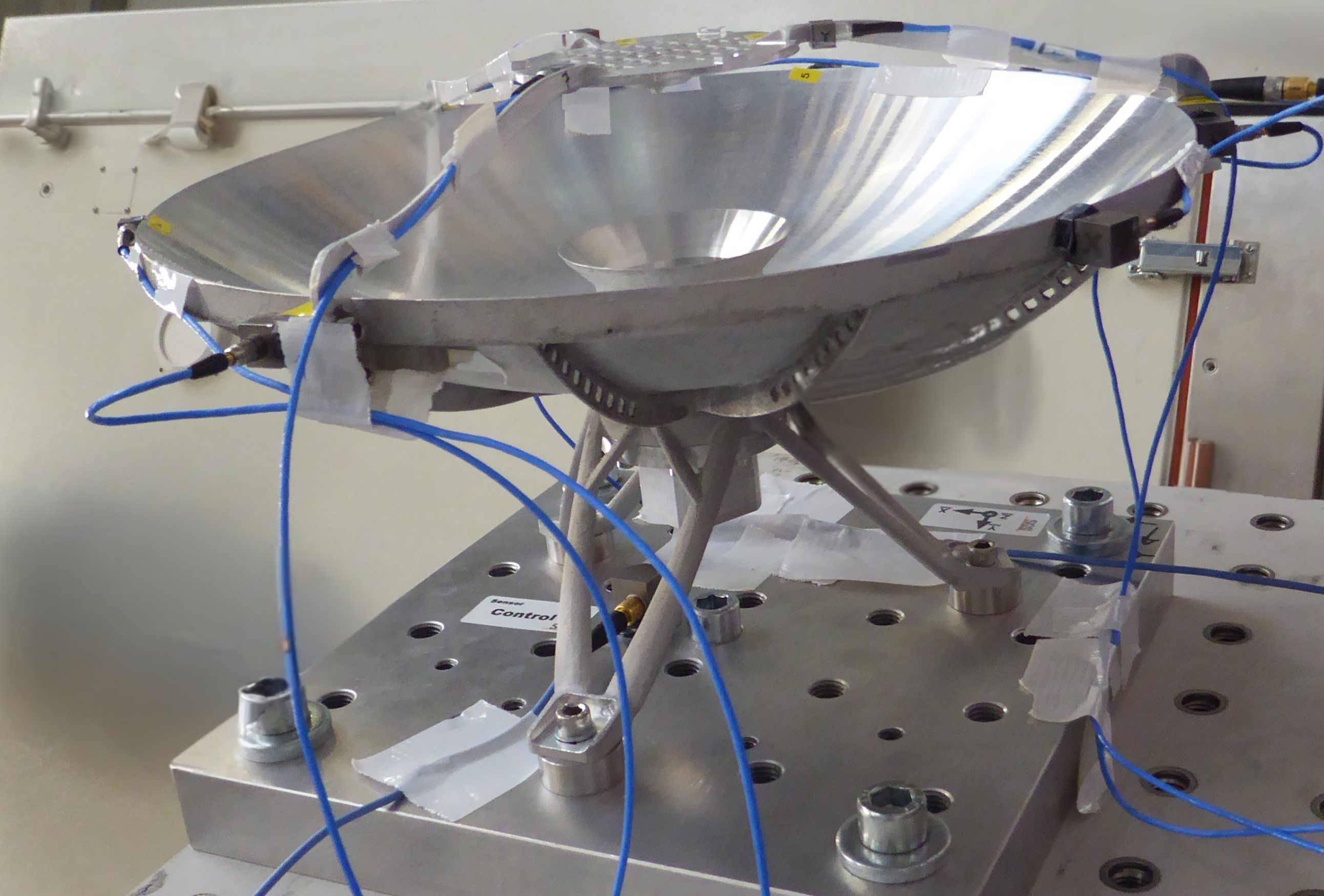
Dezember 2024
UDAN – The new generation of communication antennas for small satellites
Disruptive development by HPS for the new space sector
HPS, the Munich-based specialist for innovative antenna technology, has entered the realization phase of a fully functional engineering model (EM) with its in-house development “UDAN”. With the HPS design of a deployable conical quadruple helix, UDAN meets the requirements for the smallest possible space requirement during satellite launch as well as an antenna performance that was previously not possible on small satellites.
See deployment video from UDAN breadboard.
The pack size is only 10x10x15 cm (1.5 U), yet UDAN achieves 10 dBi minimum on usable bandwidth between 400 Mhz and 460 Mhz. When deployed, UDAN measures 50 centimeters in height with a diameter of 90 centimeters. Further scaling across the frequency ranges from 100 to 1000 Mhz is planned in order to diversify the service requirements of the communication satellites.
The development is being funded by ESA as part of the ARTES programme, while the German Space Agency at DLR is providing additional funds to maximize development efficiency.
This brings the completion of the CDR phase for February 2025, the production of the engineering model in Q2-3, followed by the test campaign and the closure of contract by Q4 in 2025. With the final completion of the project, UDAN will reach maturity level TRL 6, the in-orbit demonstration (IOD) which is planned to follow in Q2 2026 will then finally raise the HPS innovation to TRL 9 and thus reach out for the commercial market.
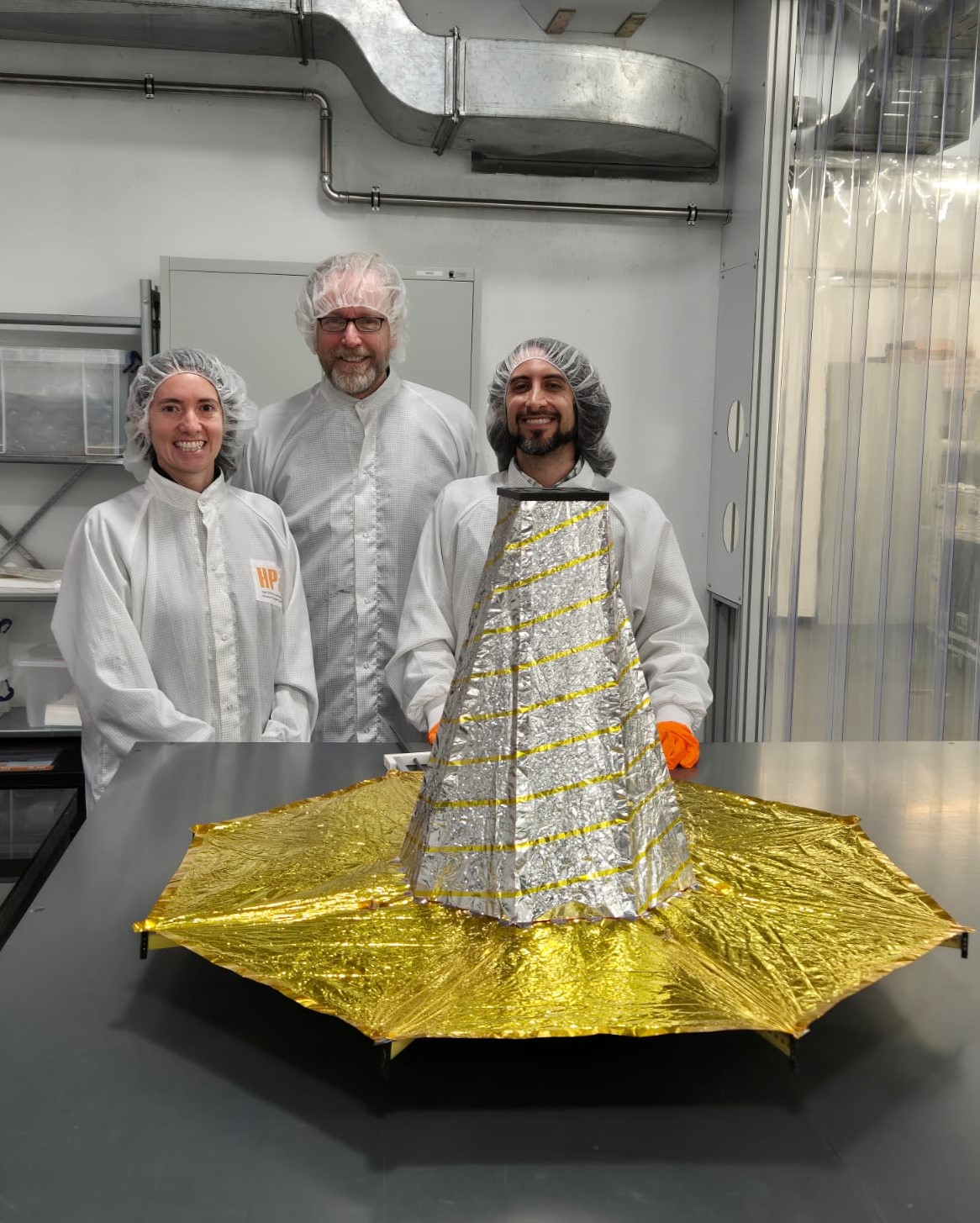
WILD RIDE mission ends with fireworks of success for deorbit sail ADEO-N2
Three days ago, on December 8, 2024, HPS received confirmation that ADEO-N2 completed its mission with launch in 2021 and end-of-business with deployment of the dragsail at 506 km orbit altitude in December 2022 in a record time of only two years with a firework of success, beating international rules and regulations by three full years. This is further proof of the success of the German ADEO model, which is manufactured in series production by the German world market leader HPS for all sizes of LEO satellites in five ADEO versions. ADEO fulfils the “5-year rule” already issued by several states and organizations for obtaining launch and operating permits for satellites, and with “Wild Ride” this has now even been verified in orbit by precisely tracking the deorbit curve until the satellite burns up completely at an orbital altitude of approx. 127 km (see image).
About the mission:
On June 30, 2021, D-Orbit, a leading company in the space logistics and orbital transportation industry from Italy, announced the successful launch of another ION Satellite Carrier (ION SCV 003), its proprietary orbital transport vehicle. It lifted off at 9:31 p.m. CEST on June 30, 2021 atop a SpaceX Falcon 9 rocket from Space Launch Complex 40 (SLC-40) at Cape Canaveral Space Force Station (CCSFS), Florida. That same day, 60 minutes after launch, the vehicle was successfully placed into a 500 km high Sun Synchronous Orbit (SSO).
ION Satellite Carrier is a space transporter developed, manufactured and operated by D-Orbit. ION is capable of accommodating multiple satellites, transporting them into space, performing orbital maneuvers and precisely releasing them into dedicated orbital positions.
At the end of the so-called WILD RIDE mission, the ION SCV 003, weighing 210 kg at the time, entered the deorbit phase on December 15,2022 with the deployment of ADEO-N2 (effective sail size 3.6 m2, christened “Show me your Wings”) entered the deorbit phase and began testing the world’s first precise functional in-situ verification of a dragsail, with official “end of flight” on 08.12.2024 [source: NORAD], i.e. within exactly 2 years in a completely natural way and without exhaust gases from any propulsion system. Without sails, SCV-003’s deorbit would have taken twice to three times as long.
About ADEO:
ADEO-N is a 1U-sized deorbit sail module developed by the German space company HPS, in cooperation with several companies and institutions (e.g. DLR and Fraunhofer), co-funded by the ESA-GSTP program, the German national technology program, and the Bavarian technology program. In accordance with the new rules, ADEO ensures the removal of end-of-life satellites from LEO within a maximum of 5 years.
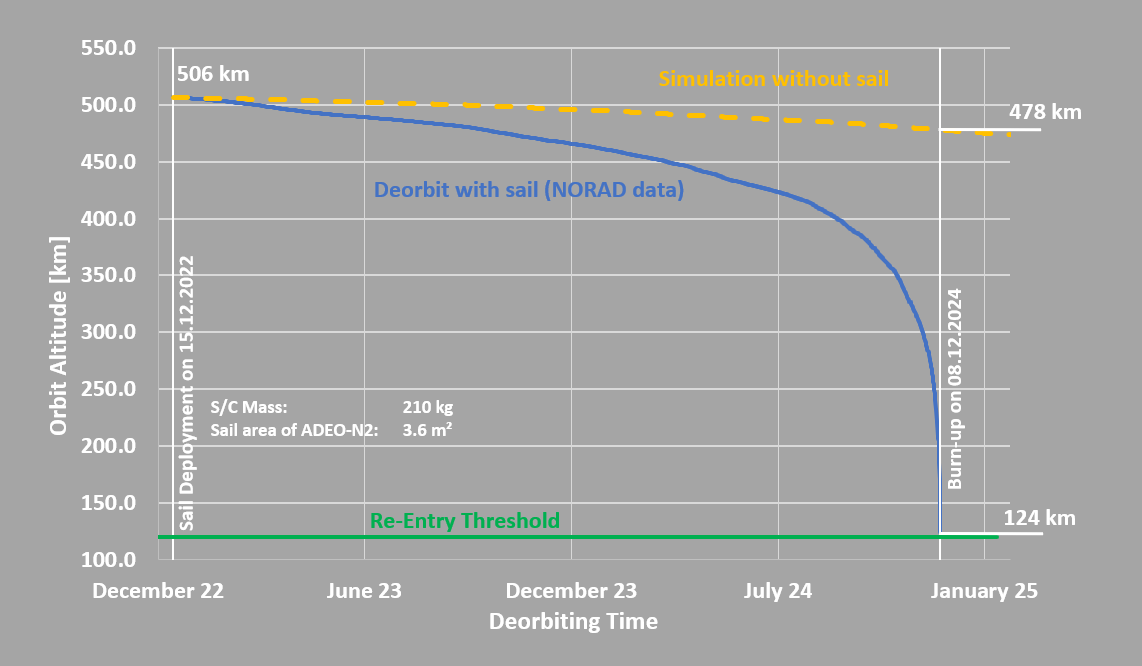
Dezember 2024
HPS Christmas Party 2024: Our Biggest Yet!
Last night, we celebrated the holidays together at our annual Christmas party – and this year was extra special!
For the first time, we hosted it on our new floor, making it the biggest Christmas party in HPS history!
The evening was filled with:
- Plenty of mulled wine and delicious food
- A variety of drinks to toast the season
- 12 inspiring mini-presentations (just 2-5 minutes each) by our Department Heads, CEO, CFO, CTO, Quality Management, HR, Procurement and Social Media, sharing insights and ideas.
It was a wonderful evening of connection, celebration, and looking ahead to an exciting future. Here’s to the amazing HPS team and the bright year ahead!
Producing antennas in series
For over 20 years, the Munich-based space technology company HPS has been known for breaking new ground wherever possible and establishing an increasingly solid bridge between ClassicSpace and CommercialSpace with innovations of all kinds. This applies to products such as deployable antennas of all sizes through to processes such as the series production of the deorbit sail module product family (ADEO).
With the implementation of a further process innovation, HPS is now also realizing new efficiency horizons in the antenna sector, because a commercial customer is in a hurry: more than 20 broadband antennas are needed, in a period of less than only 12 months, starting NOW. HPS is already known from a large number of successfully completed antenna orders – whether from the institutional or commercial sector – for the routine of quality production at a consistently high level that is valued by customers. But now, with the start of small series production, the company is heralding the introduction of a further development stage in the process of merging the quality features of conventional and new space technology into something new and even better. And despite all the high pressure, with the power that comes from calm.
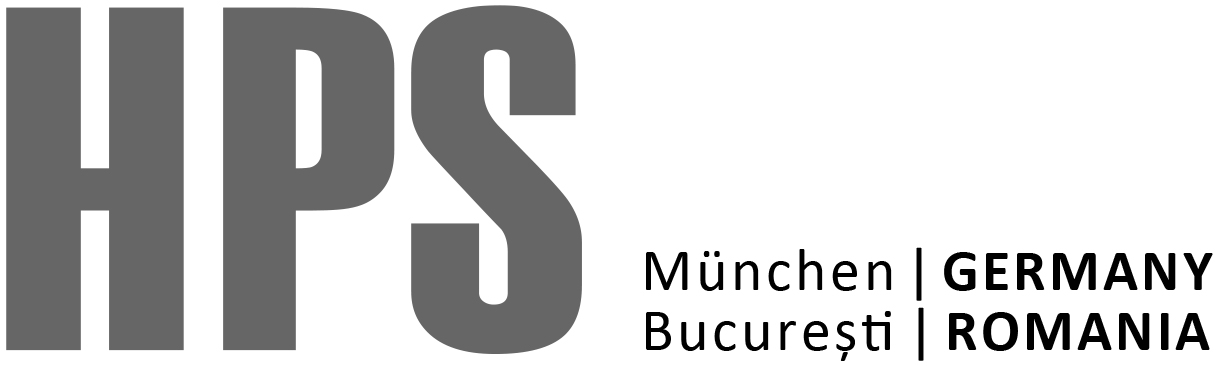
November 2024
HPS and EXOLAUNCH: Making Space Clean Again
HPS is happy to join forces with the Germany-based Exolaunch and is fully engaged to support customers of Exolaunch by enabling this very special and successful NewSpace-launch service provider to grant priority access to the delivery schedule of flight-proven ADEO* deorbit sails which are currently in high demand.
EXOLAUNCH’s COO Jeanne Allarie and HPS’s CEO Ernst Pfeiffer signed an Agreement on Space Tech Expo 2024 in Bremen in a great joint spirit (see pictures) the ambitious endeavour of
- being a role model for a sustainable use of space and
- of raising awareness with all potential customers on an existing solution for deorbiting: ADEO-modules are easy, affordable and reliable to contributing significantly to Making Space Clean Again.
See for the respective EXOLAUNCH announcement
(* ADEO-modules are needed to allow a satellite deorbit after its “End-of-Business” within five years; satellites without this or any kind of deorbit accelerator do not get clearance for launch anymore.)
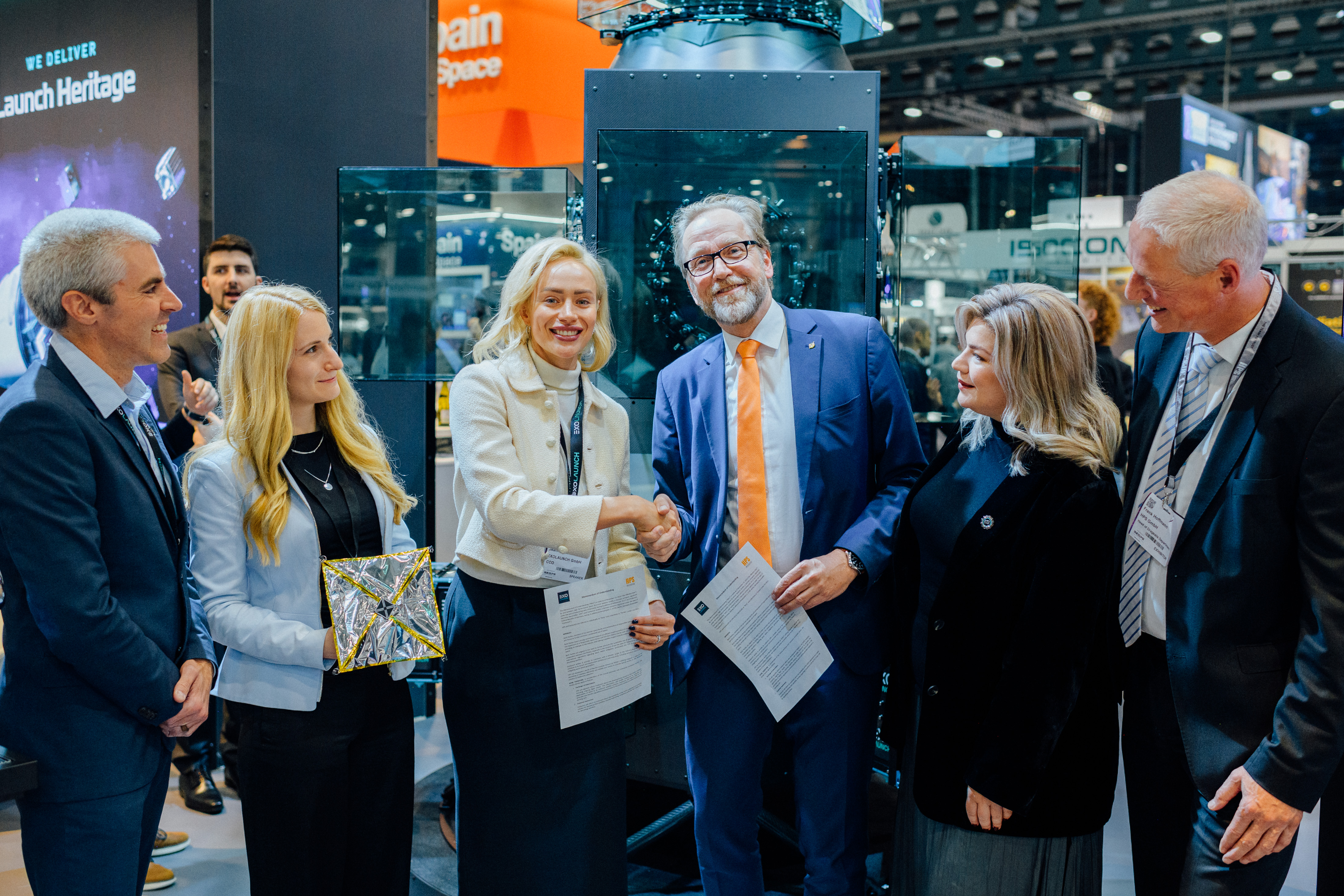
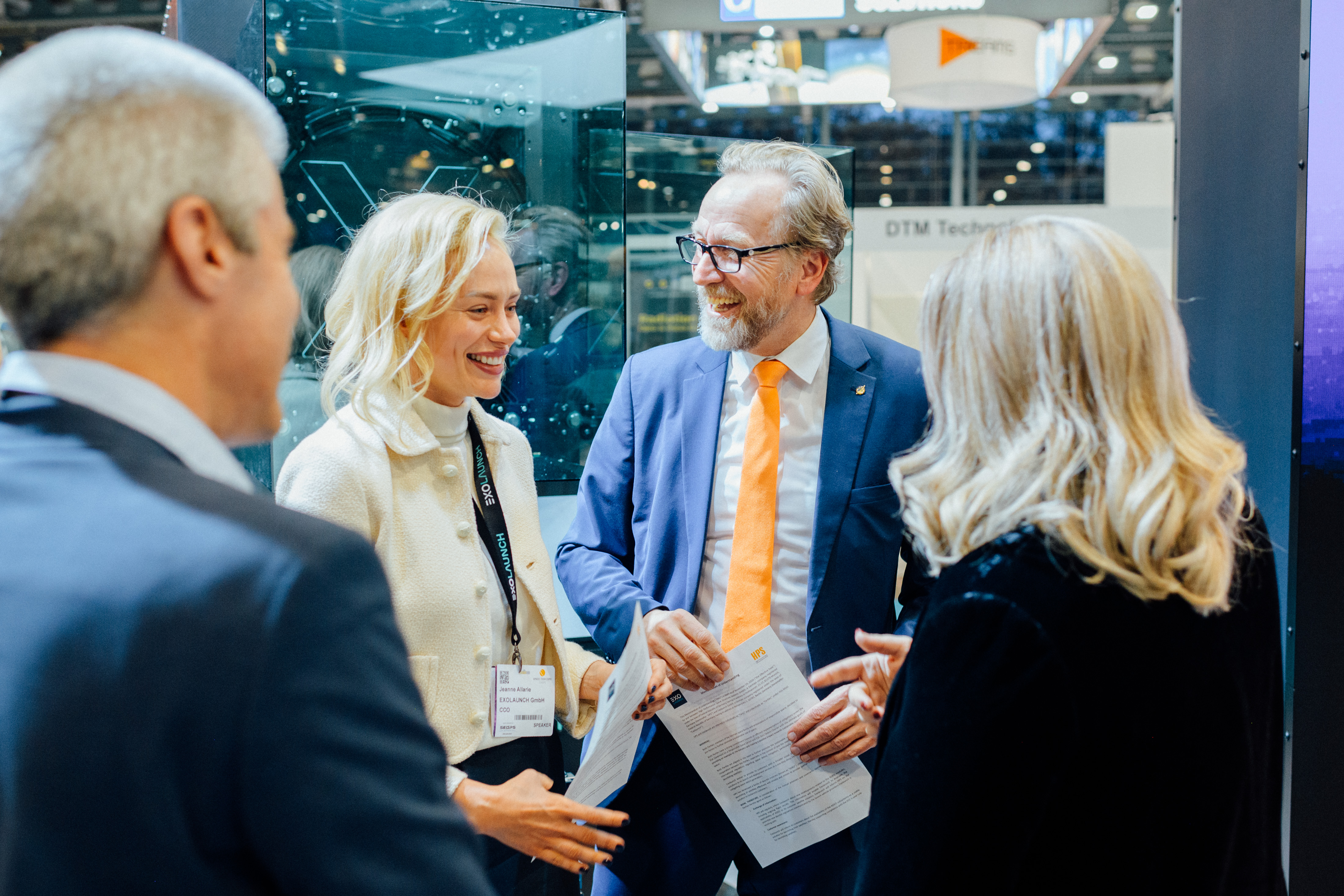
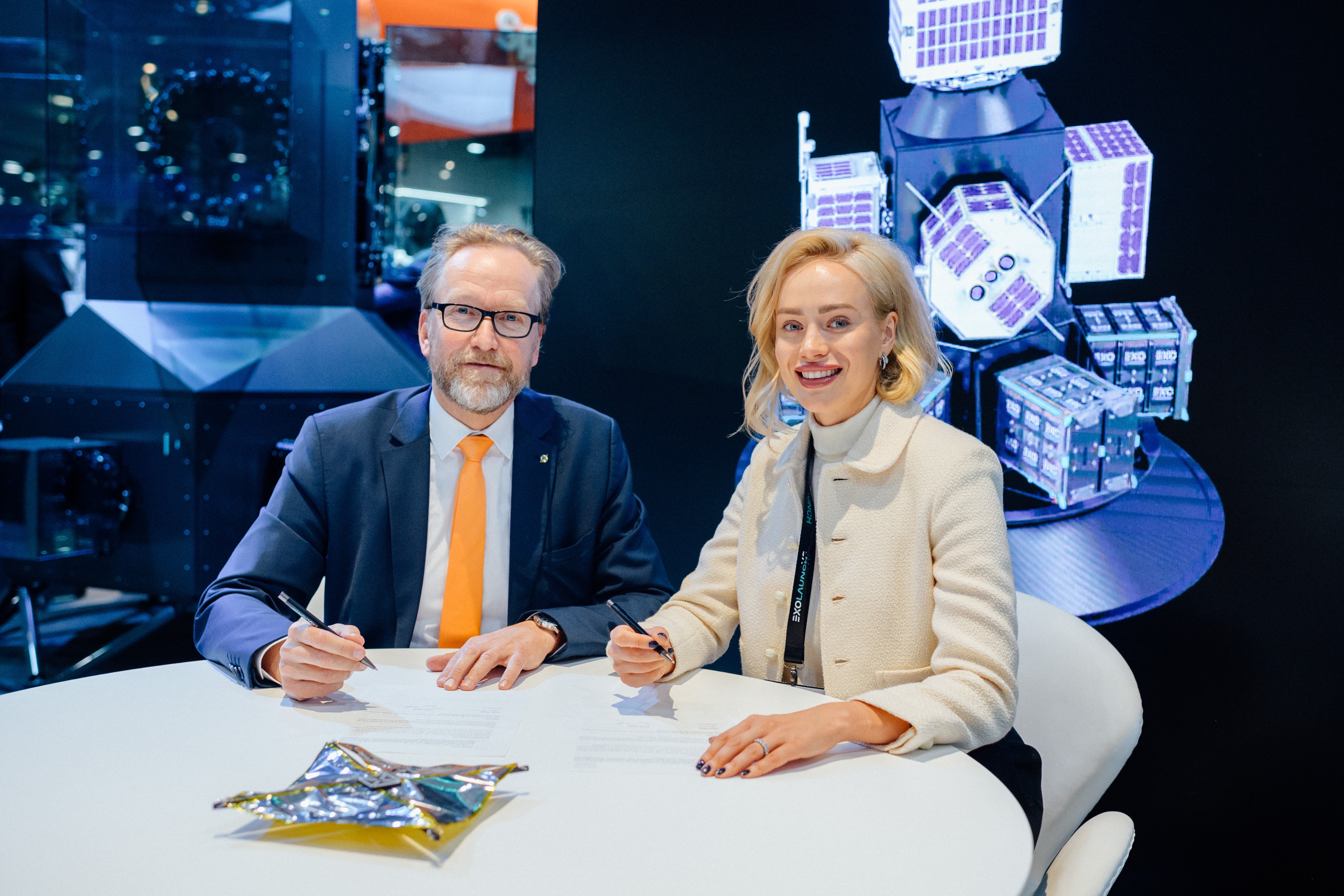
November 2024
German space agency chief Dr. Walther Pelzer and DLR delegation focus on visit to HPS Group
During the traditional DLR delegation round on the opening day of the Space Tech Expo in Bremen, the head of the German Space Agency at DLR, Dr. Walther Pelzer, focused his attention on SMEs in the German space industry. Special attention was paid to the innovation forge HPS. And it was represented in groups: with HPS Germany (Munich), HPS Romania (Bucharest) and the joint venture company HPtex (Münchberg, Germany).
With reference to pioneering antenna projects such as HERA and EUCLID, company boss Ernst K. Pfeiffer emphasized the leading position Germany has gained in special antennas for space missions. HPS is also positioning itself as a leader in the commercial sector with the successful ADEO braking sail project, which ensures compliance with the new 5-year rule for satellite deorbiting and thus keeps the satellites ready for launch.
In his role as spokesman for German space SMEs, Ernst Pfeiffer also took this opportunity to emphasize the enormous importance of the DLR and ESA’s capability-enhancing technology programmes for SMEs as the innovation backbone of the industry. According to Pfeiffer, the precise promotion of the technological capabilities of SMEs via dedicated competition areas reserved for SMEs is irreplaceable.
Live demonstrations, e.g. of a functional model of the ADEO brake sail or a scaled model of a deployable large antenna reflector, supplemented by product demonstrations from HPS-Romania (e.g. radiator) and from HPtex’s MESH production (e.g. Ka-band mesh sample for use in the Copernicus mission CIMR) rounded off the visit program.
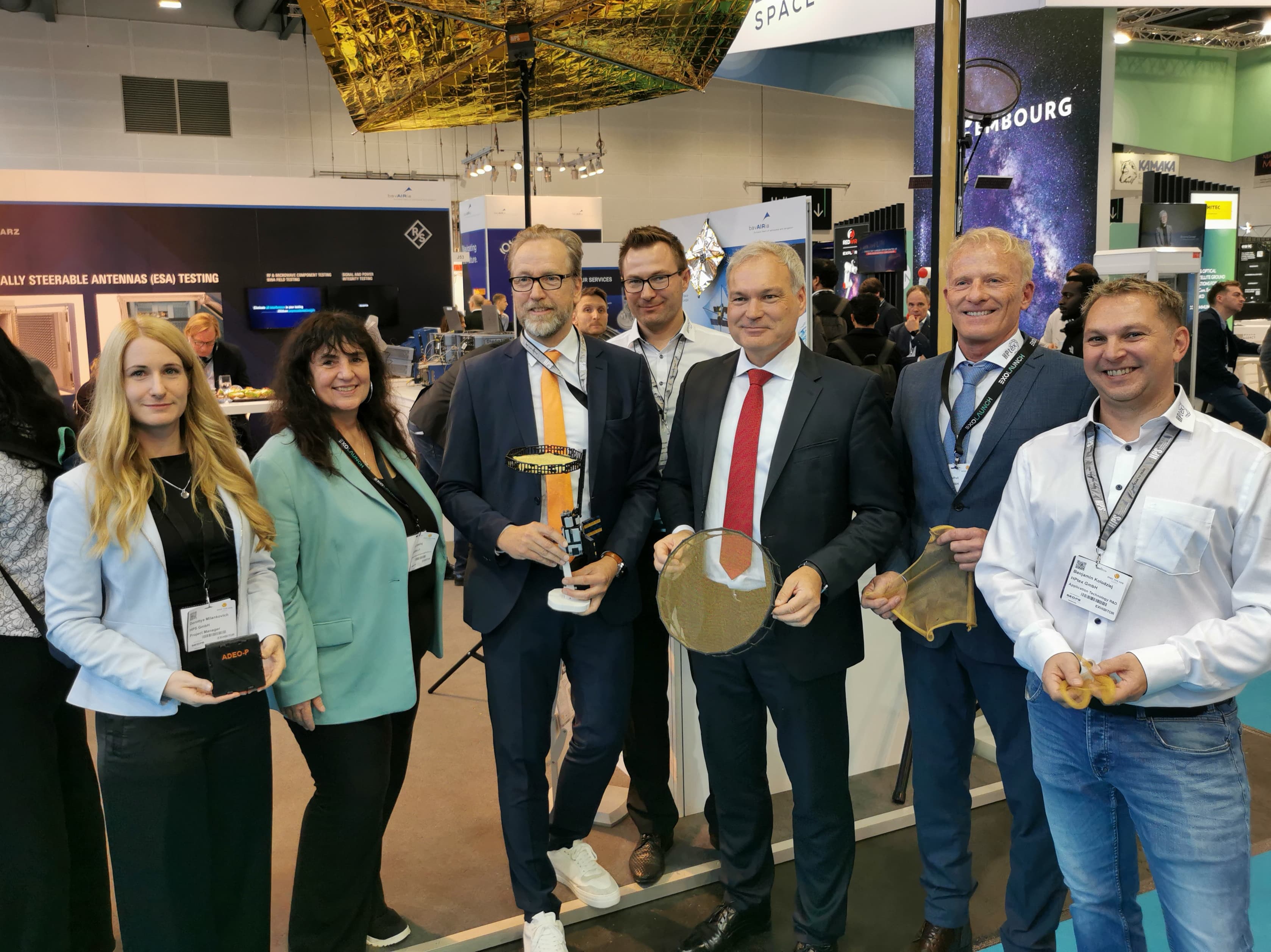
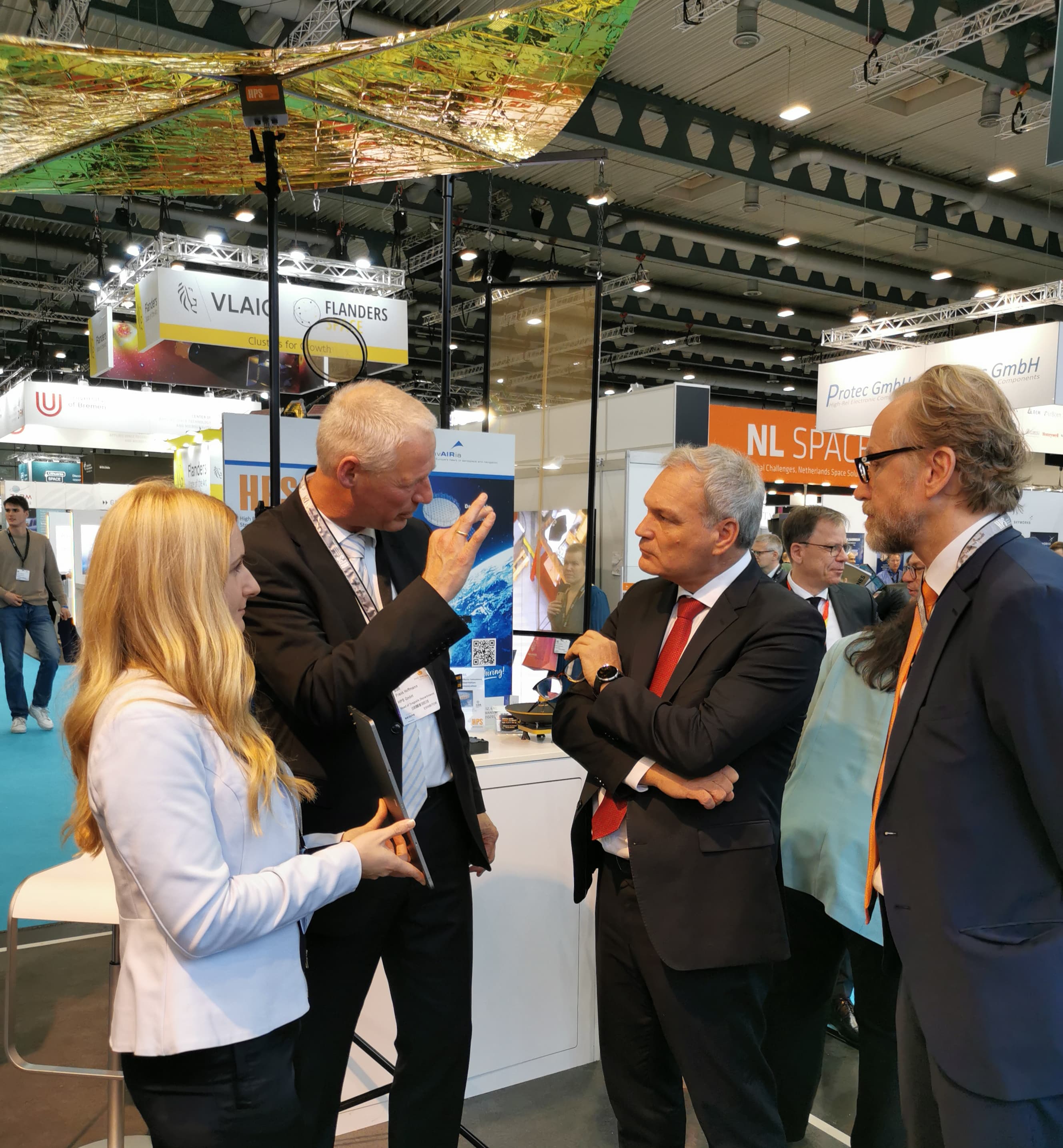
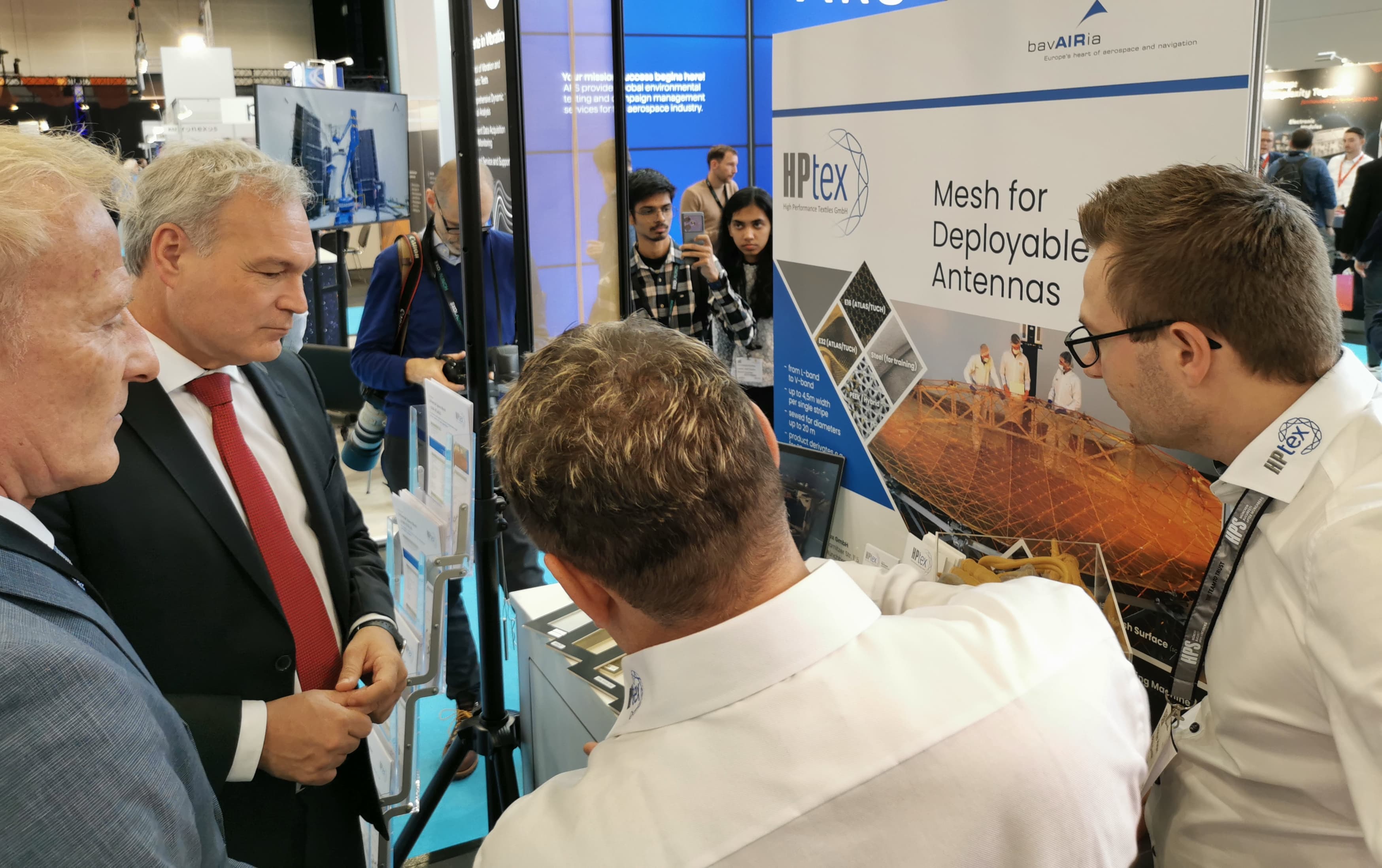
HPS at Space Tech Expo 2024
November 2024
HPS at SpaceTech Expo Bremen: Full product portfolio of the entire group of companies at the presentation area of the Bavarian space companies (booth no. J53)
In record time, SpaceTech Expo in Bremen has developed into the largest and most important space trade fair in Europe. This year’s event has over 700 exhibitors. With its rapid growth, SpaceTech Expo in Bremen is itself the best example of the rapidly increasing importance not only of space capabilities in general, but also of the young NewSpace companies that are making powerful inroads into the commercial and institutional markets for space products and services.
However, a very special role is played by those companies whose portfolio serves both the New and Classic Space sectors, thus building a bridge between the two in-house. One of the most prominent examples is the HPS Group.
This innovator in European space-tech, with its headquarters in Munich, subsidiary HPS Romania in Bucharest and joint venture partnership HPTex in Münchberg near Bayreuth, is bringing all the product evidence for this positioning to Bremen.
For example, institutional customers looking for European solutions for large deployable reflector subsystems will find them at HPS, which will ideally play a constitutive role in upcoming iconic ESA earth observation missions such as “Cryorad” and “Hydroterra”.
The heart of these subsystems is also produced in-house: HPTex GmbH weaves reflective mesh surfaces of all sizes for deployable antennas. In addition, HPTex – with its own stand in Bremen now for the first time – even produces stainless steel mesh for training purposes for customers from all over the world.
Two representatives from Bucharest will also be present in Bremen; the main focus here will be on secondary structures, thermal hardware (MLI, thermal straps, radiators), MGSE and purge equipment. All products are scalable for large missions as well as for small satellites and cubesat missions.
However, literally “floating” above the overall portfolio of the HPS presence in Bremen is the star product of HPS, which is currently causing a worldwide sensation like no other, especially interesting for customers from the NewSpace scene: ADEO, the brake sail for the automatic controlled deorbiting of disused satellites of almost any size at the end of their mission. The reason for the ADEO hype is as simple as it is obvious: without technical equipment to guarantee a deorbit limited to a maximum of 5 years, satellites will no longer receive approval for launch on LEO. One technical option is the “manually controlled” descent. However, in addition to considerable personnel resources, it also consumes up to 60 percent of the fuel that should actually keep the satellite in orbit for as long as possible so that it can earn its money in the first place. The other option is to install a deployable brake sail on the satellite at the end of the mission, which then automatically brings its host “home”. The industrial world market leader for this technology on all continents is HPS from Munich; a live demonstration of the deployment of a PICO-class ADEO will take place at SpaceTech Expo at a date yet to be determined. This could be a highlight for all interested new customers. The flood of inquiries about prices and interfaces speaks volumes.
HPS CEO Ernst K. Pfeiffer himself will be on site for the entire duration of the trade fair alongside the management level of the group from Romania and Germany; he has a firm opinion on the event both as the company boss and as a spokesperson for SMEs in the industry, represented by the AKRK and the “Best of Space” association: “Europe’s non-dependence and sovereignty through its space industry is more important than ever before, especially after the presidential election in the USA. What we will see here in Bremen is the antithesis to the far too widespread phlegm of a bureaucratized industry and to the “we can’t do anything anyway” attitude that has been creeping in for some years now: fresh ideas, brashly and cheekily driven forward – that’s what space travel needs, including the “Made in Germany” seal. NewSpace and Classic Space are mutually dependent and stimulate each other, because even the most disruptive developments need to be anchored in the familiar and proven. This is also what we at the HPS Group stand for.”
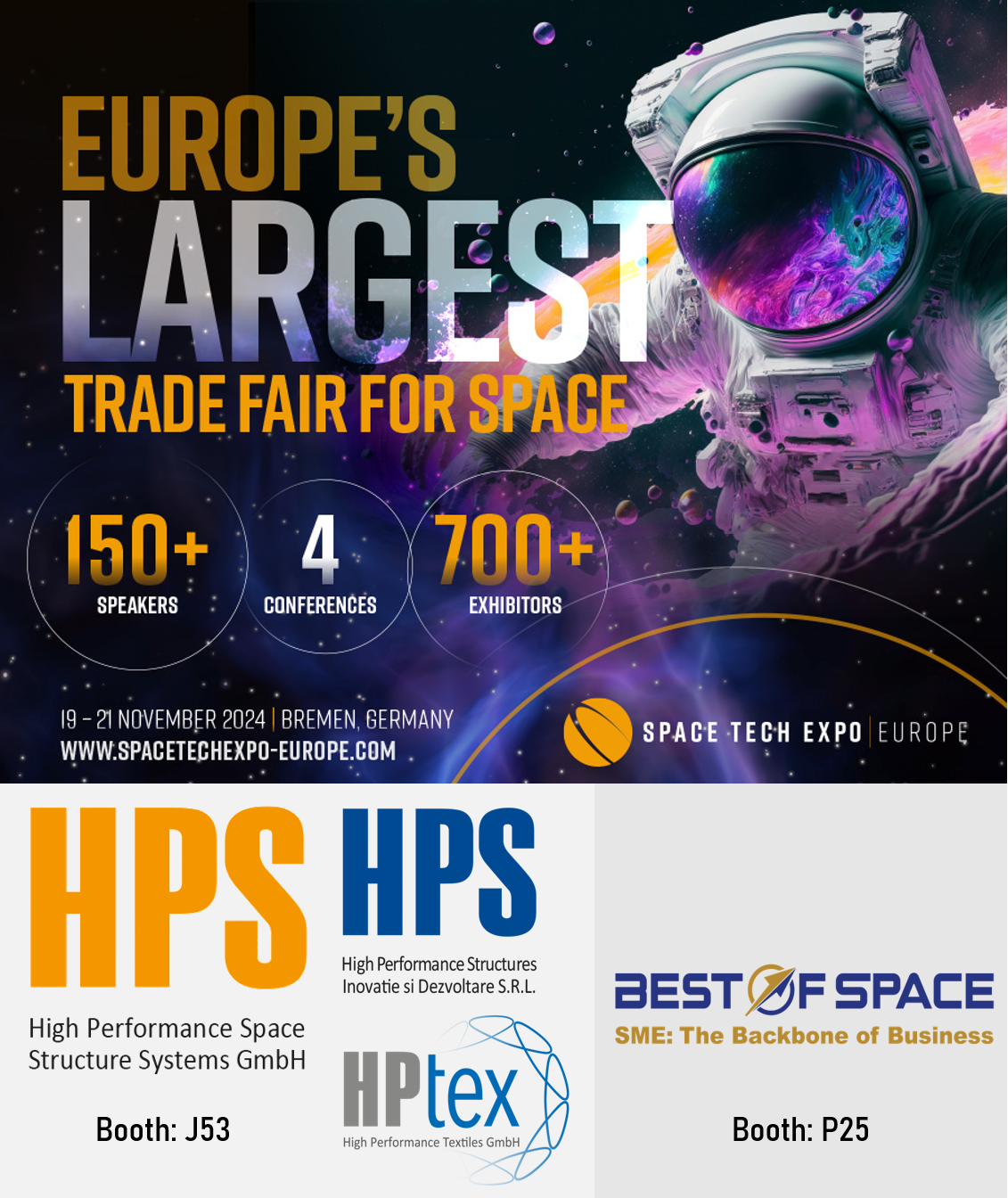
November 2024
New laboratory for mesh research at HPS
The Munich-based space technology company HPS is a joint venture partner of Iprotex-GmbH; both are equally involved in the joint company HPTEX in Münchberg near Bayreuth. This is where the flexible reflector material “MESH” is tailor-made and of the highest consistent quality for applications such as small and large deployable space antennas.
The market for mesh is divided among a small number of players worldwide. To survive here, continuous development is an essential prerequisite. HPS has therefore recently set up its own mesh research laboratory at its Munich headquarters on Hofmannstrasse. The initial team of two specialists is currently being expanded to include a further engineering position. The initial equipment of the laboratory for the further development and optimization of HPTEX mesh has already cost HPS 50,000 euros; among other things, investments were made in a mesh tension jig (stretch test rig) including an HD camera system. In addition, for yet another 50k euros the whole basement-area of the HPS building has been improved to host capacities for assembly work on ADEO brakesails in serial production.
Customized service is a top priority at HPS, so the new laboratory also carries out contract research, e.g. in a project called VMESH, in which a mesh for the very high frequencies in the V-band is being developed. The laboratory’s ability to carry out multiple iterated processes to measure the stretchability of antenna meshes is also unique on the market.
In addition, HPS is Europe’s only supplier of large deployable antenna subsystems with its own mesh production. The company’s flagship project is the ESA Copernicus Mission CIMR. HPTEX also serves customers from all over the world, including Europe, the USA, the United Arab Emirates, South Korea, Singapore and Taiwan, with the support of the new laboratory at HPS. The mesh is manufactured at HPTEX itself.
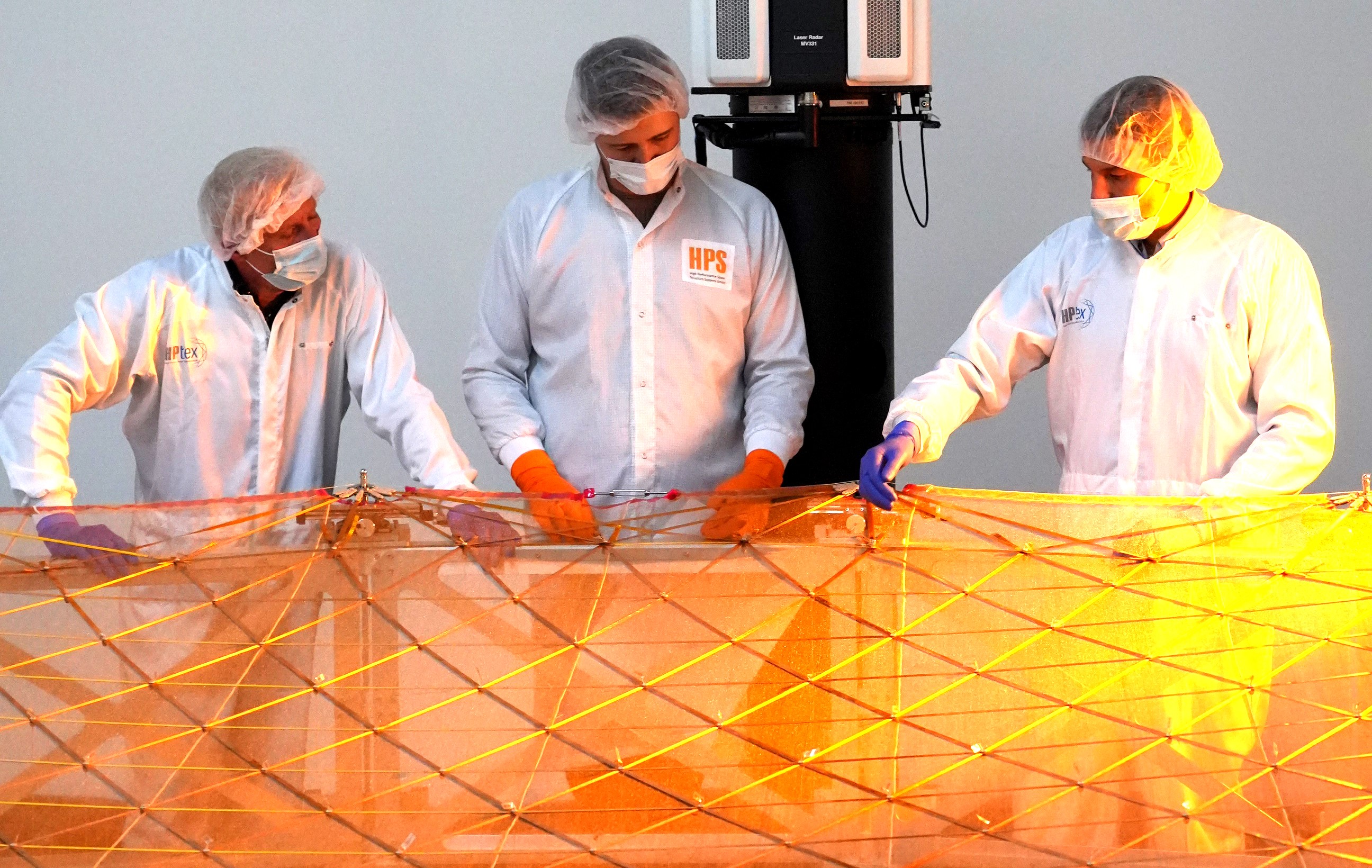
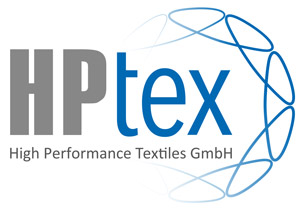
October 2024
Clean Space Days der ESA im Oktober: ADEO aus dem Hause HPS im Fokus
In 2024, the ESA’s Clean Space Team once again invited participants to the continuation of the past Clean Space Days.
The four-day event will focus on progress in the areas of eco-design, zero debris and in-orbit maintenance.
The calendar of presentations in 2024 will highlight these topics, among others:
- Life cycle assessment for space activities
- Deorbit technologies
- Debris disposal
- Disturbance-free skies for astronomy
- IOS missions
- Circular economy for space travel
While some presentations tended to highlight ideas and technical concepts in statu nascendi, HPS manager Frank Hoffmann presented the ADEO product family, which is already successful on the European and, more recently, North American markets: Deorbit sail technology for automatic self-disposal of the satellite at the end of the mission.
The ADEO system offers a suitably customized solution for every class of spacecraft, whether as a “Pico” (1-20 kg), “Cube” (5-50 kg), “Nano” (20-250 kg), “Medium” (100-700 kg) or even “Large” (500-1500 kg). To ensure that satellite manufacturers are supplied without delay, all orders are handled by HPS directly from series production wherever possible.
Due to the fact that the requirement to carry a suitable disposal system such as ADEO is a prerequisite for launch authorization for practically all satellites from October 2024, longer delivery times are possible and can be largely avoided by ordering early.
The Clean Space Days will come to an end at the end of the week, but the saying “after the event is before the event” also applies to this successful European space event.
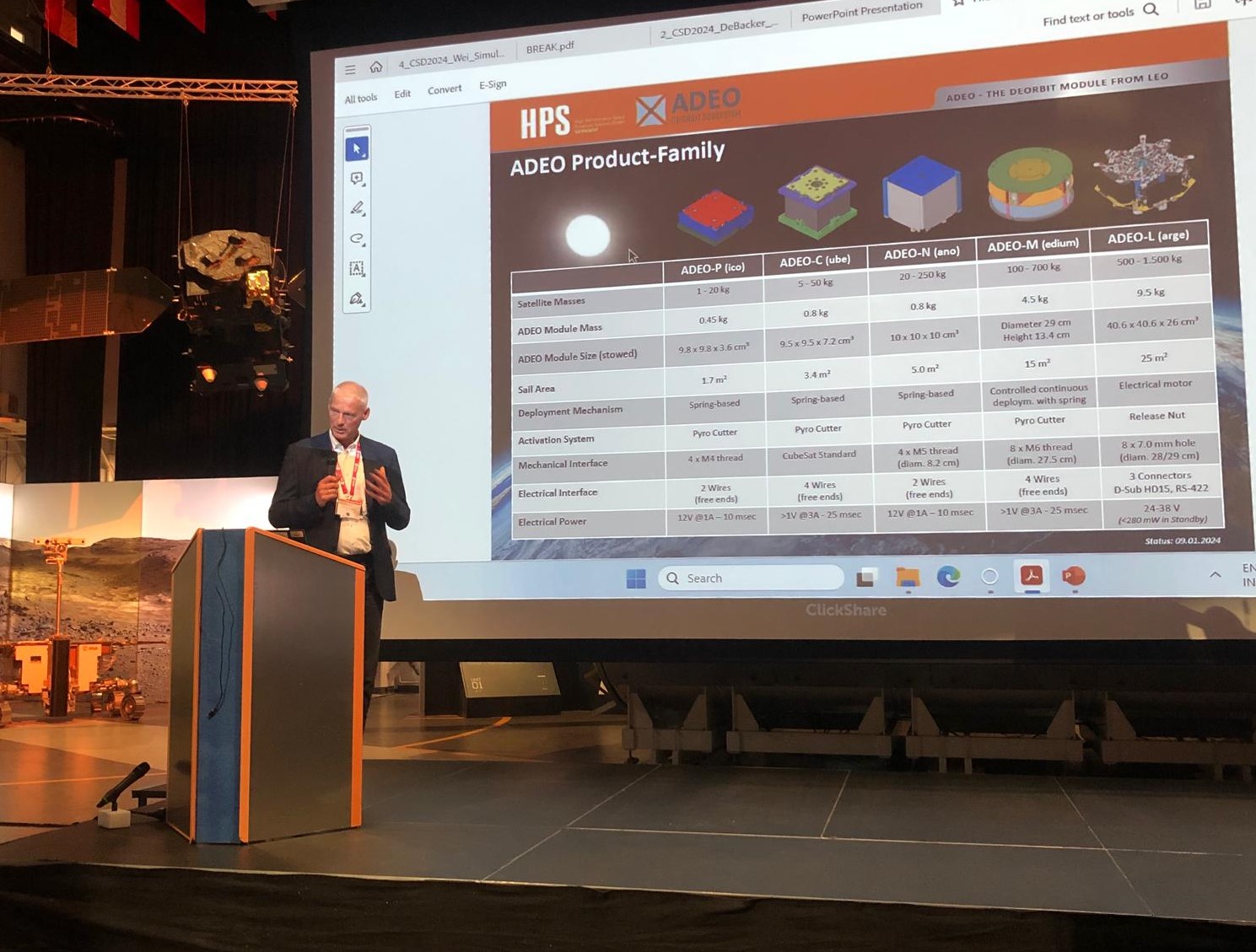