Electronic Housing
Since 2005 HPS has continuously developed CFC-based technologies in the context of national and ESA-programs in order to replace unnecessarily heavy and expensive aluminum housings for electronic equipment by electronic housings made of carbon fibre composites.
Ten years of constant development have made HPS Europe´s number one as provider of CFRP-electronic housings manufactured serially as well as on special demand which
- considerably save weight and costs
- decidedly improve accuracy on satellite-level by avoiding distortions due to differing coefficients of extension, for example in satellites for earth observation purposes with pointing requirements.
CFRP-electronic housings made by HPS come up to the following demands:
- increased thermal conductivity in comparison to aluminum with 220 (W/mk), verified through many thermal tests, also including vacuum conditions
- compliance with EMC-requirements by adding carbon naotubes (CNT) and by special treatment of edges, verified through EMC test campaigns
- verification of vibration impacts through test campaigns.
- Customized high energy sheelding by inserting tantalum foils into the CFRP laminate
- Possibility of using COTS components.
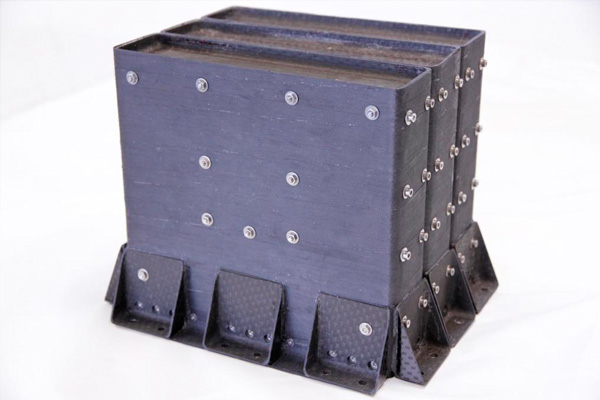
Contact:
For further information please contact our chief engineer.
References:
→ Success Trajectory
Housing for Space Applications
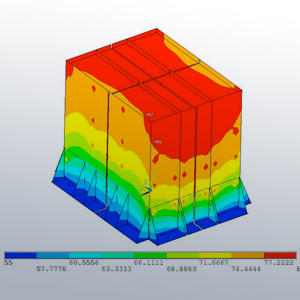
Features:
- Conduction of heat of electronic boards via
highly conductive CFRP fibres and specific fibre orientation - Modular approach for standard PCBs and larger electronics
- Custom made housings for smaller electronics and series production
- Eigenfrequency > 140 Hz
- Mass reduction: 10–30 % (depending on radiation shielding requirements)
- Primary application targets: series production electronics for telecom and tailored housings for planetary missions
Housing for Aircraft Applications
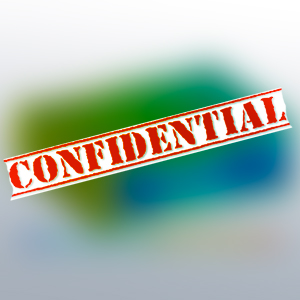
Primary goal: mass reduction, which means propellant reduction over aircraft‘s lifetime.
Features:
- Cooling of electronics via convection of air around cooling fins
- External interfaces to aircraft can remain the same
- Modular approach for several electronic sizes
- Mass reduction: 20–30 %
- Unit price strongly dependant on performance requirements and in consequence on material selection