HPS puts ADEO know-how at the service of ESA´s Hungarian Prime C3S
ESA-project SAILOR: Shots on sails to detect untraceable debris
It seems to be a basic law of nature: Wherever and however humans are active, they end up producing large quantities of waste. To suppress the problem, many terrestrial areas, the oceans and, in recent decades, outer space itself have become dumping grounds. However, the latter in particular is now threatening to take radical revenge, as flying debris from previous space missions is increasingly becoming a threat to all other activities, especially in the most frequented orbits between 200 and 1200 kilometers.
While large debris such as burnt-out rocket stages are the easiest to detect and can be avoided by new guests in orbit, it is the small projectiles, flying with 5-10 km/s orbital speed, which have often shrunk below millimeter size as a result of previous fragmentations, that pose the greatest threats. Even one millimeter-sized debris impact can render a satellite inoperable. Emerging their threat further, their flux increases significantly as their size decreases, with the consequence that the much more frequent impacts of debris of this size can pose a far greater risk to space operations than the more dramatic catastrophic incidents.
However, only larger debris can be observed and tracked from the ground – but not in the critical range of 0.1 to 50 mm. Therefore, measurements in situ, i.e. directly in orbit, are urgently needed to make it possible to describe the Earth’s flying garbage dump with sufficient reliability in the first place. After critically weighing up the alternatives, ESA has turned its attention to a possible large-area detector based on the successful ADEO deorbit sails from HPS. If the sail membranes are now equipped with acoustic sensors and cameras on board, it will be possible to measure the dust flow in the required size range. The name of the project: SAILOR – Sail Array for Impact Logging in Orbit.
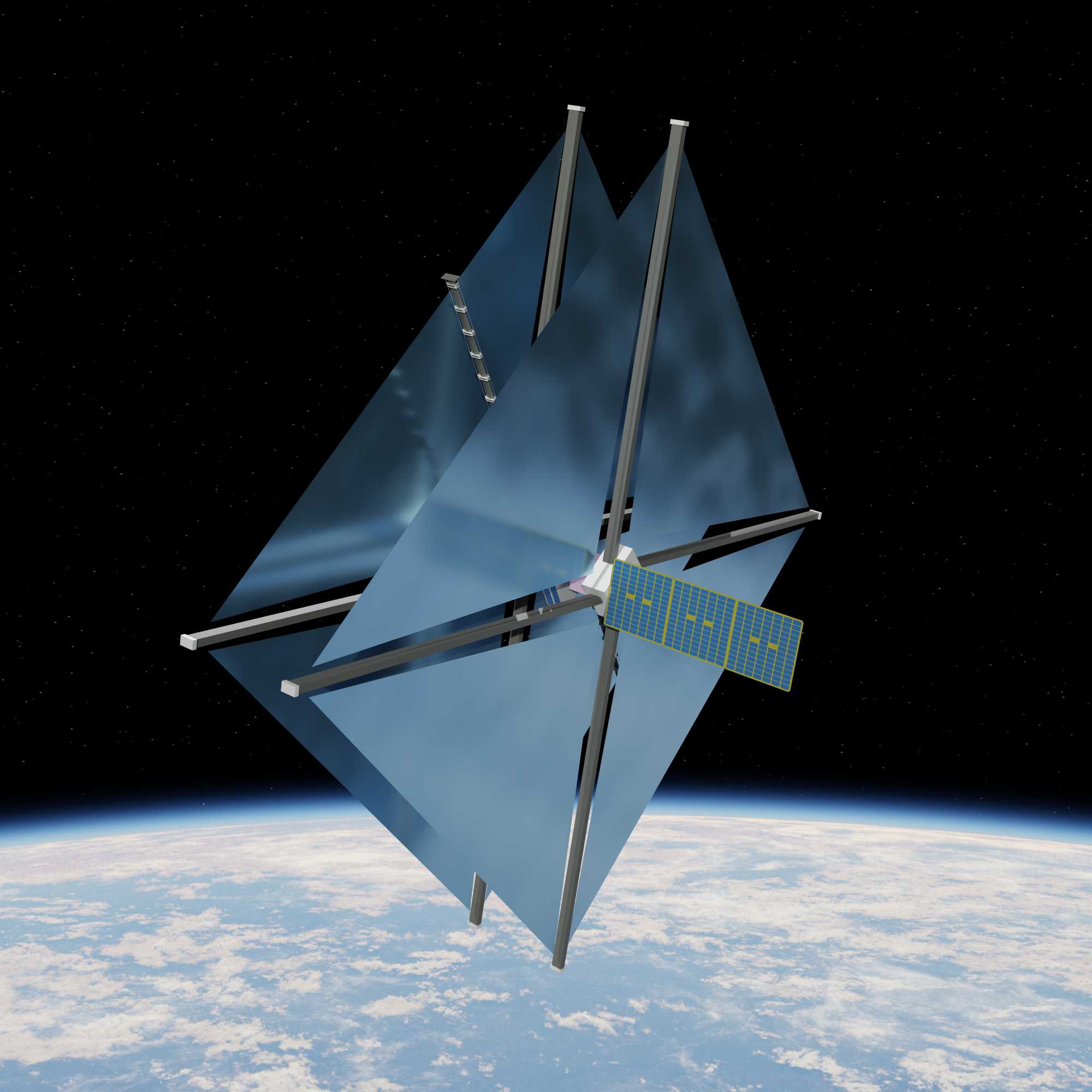
The spacecraft consists of two large detector surfaces 100 cm apart. The two sails have an exposed surface area of 25 m2; in the ADEO program, they are the main actors of the large dragsail versions under the name ADEO-L. The membranes are around 10 μm thick and are held in position by extendable cross booms. The booms are stowed together with the sail membranes during launch and deployed in orbit. The deployment module in which booms and sails are integrated, consists of a deploying mechanism with a motor that pushes the boom arms outwards. A system of multiple cameras is mounted to a separate boom to document the holes created on the inner surface of both sail membranes. Acoustic sensors are attached to the sails to detect an impact in real time. The interaction of SAILOR’s technical equipment will ultimately allow the density, speed and trajectory of the small debris to be determined.
The ambitious ESA project SAILOR is currently in the transition from Phase A to Phase B1, which will also include the construction of breadboard models of the spacecraft and its electronics as well as the associated test programs. It also involves these steps:
- Production of test samples of the proposed membrane equipped with the acoustic sensors
- Tests of sail folding for stowage
- Testing of the boom and sail deployment mechanisms
- A high-speed (hypervelocity) impact test program to test the sails and sensors
- Testing a camera system to image holes in the sail
- Preliminary design of the spacecraft including suppliers for all critical components and subsystems. PDR is currently planned to be achieved until 2028.
Overall, the specifications of the project in this phase should lead to a positive decision at the ESA Ministerial Council meeting in Bremen in November 2025 on the continuation of a three-year mission at an altitude of 850 km to be launched in 2031/2032. The industrial team proposes a small precursor CubeSat mission, called OPTIMIST after this type of sailboat, to test the sensor technology using an approx. 10 m2 membrane as early as 2027/2028 as risk mitigation for the full-scale mission.
The industrial structure behind SAILOR also stands for this. This is because C3S, a leading Hungarian aerospace company, is acting as prime contractor for an ESA project of this kind for the first time, drawing on the expertise of ADEO inventor HPS GmbH as a subcontractor for the deployable membrane subsystem. C3S is also planning work shares for HPS in Romania. HPS CEO Ernst K. Pfeiffer: “The great enthusiasm with which we have taken on our role in this project rests on three pillars: firstly, it is existentially important for the space industry as a whole; secondly, it is an opportunity for us as HPS to impressively demonstrate the versatility of the ADEO technology from our company; and thirdly, we consider it eminently important in Europe that the industrial talents of Hungary and Romania are finally brought to light in an appropriate way, and that in a joint mission. We at HPS are delighted to be working under the project management of C3S.”